OPEX ASSESSMENT ROUTINE
ASSESS YOUR FACTORY'S OPERATIONAL
EXCELLENCE CULTURE
1. LEARN BY YOURSELF & CHALLENGE YOUR WAY OF DOING
WHY
The OPEX Assessment is the GPS of the organizations willing to sustainably improve their performances. It gives the position on the journey toward Operational Excellence.
At first, an assessment allows the organization to determine its starting position (line by line & global). Then the organization will rely on the Assessment grid to define its target, and build its action plan. Finally all along the way, thanks to regular Assessments, the organization will measure its progress & check if still on the defined path. Learn more about CICA competency
WHAT
An Assessment is an event (The Assessment) during which an assessor evaluates the organisation regarding a referential (The Assessment Grid). It provides a fair evaluation of the situation at the time of the assessment. It allows the assessed organization to be positioned on the grid, highlighting strong points & points to improve regarding the referential or a defined target. It is as well a privileged moment of coaching & alignment between the referent (assessor) & the assessed organizations.
BENEFITS
In any cases, assessment from internal (one department assessing an other department) or from external, on full or part of the organization, on one or several criteria:
-
The assessor develops his Industrial & Operational Excellence cultures, discovering practices, environments, people and coaching customers (assessed organizations) on the understanding of the Continuous Improvement Implementation.
-
The assessed organization gets a priceless appraisal from an external, allowing taking a step back, making a new start or readjusting the path.
-
Self-assessment has to be done collectively… and is not a piece of cake. The benefit remains in the alignment of the different team-members regarding the sense, the current situation, & the raising of a shared action plan. A time to time external assessment remains necessary.
HOW
The Assessor plans his Assessment with the organization (date, persons to meet, agenda, perimeter & topics to assess).
The D Day, after an opening meeting, he, together with some representatives of the organization, leads a walk on the field, observing, interviewing, gathering facts & data.These elements allow him to evaluate the content of the different boxes of the grid, & to provide an evaluation.
The assessment covers a perimeter (full or part of the organization), and will explore full or part of the repository.
Following the observations, there will be a first sharing at end of the day. Then the assessor will send a fair report including evaluation & facts which lead to the result. The report doesn’t content any advice or proposal of improvements.
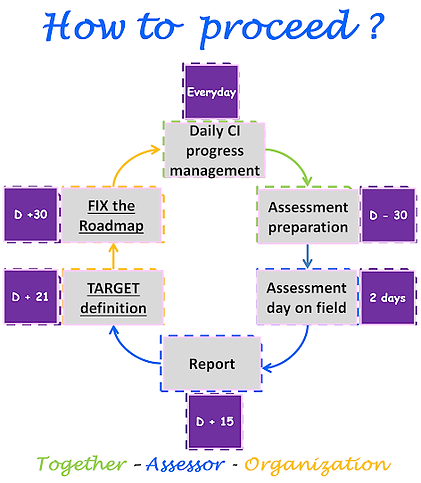
The DMW platform provides you the necessary learnings material (sense + good practices + coaching...) to go toward excellent manufacturing and build your own routine.
Below find all the connection between opex lines and DMW cards.
Axis 1: Promotes the change toward a sustainable self-improving organization (C)
Axis 2: has developed a problem thinking culture (P)
-
P1 = Visual Management (visual factory + 5S management + Internal communication)
-
P2 = Performance boards (perfs boards - perfs indicators - visual factory)
-
P3 = Performance indicators (perfs boards - perfs indicators - visual factory)
-
P5 = Problem detection (Andon system)
-
P7 = Problems management culture (Kaizen system - Benchmark strategy)
Axis 3: focus on the empowerment of its team members (E)
-
E1 = Sense & Values (core values - Factory purpose - exemplarity of managers)
-
E5 = Job & Roles description (job description - Factory structure)
-
E6 = Training system (learning system - training center - standardized work)
-
E7 = Ideas system (kaizen system - innovation)
-
E8 = Skill management (multiskill management)
-
E9 = Teammates happiness (collective meetings - Happy teams)
-
E10 = Teams size (factory structure)
-
E11 = Towards autonomous teams (factory structure)
-
E12 = Teammates development (development of people - job trekking
Axis 4: continuously optimizes its value chains "to satisfy its customers" (O)
-
O2 = Management of the value chain (Wastes identification - Value chain mapping - MIFD)
-
O3 = Basic stability: Working envt (5S Management - visual factory )
-
O4 = Basic stability: Man (visual factory - safety & ergonomy - Absenteeism management - production line optimization)
-
O5 = Basic stability: Machine (Machine maintenance)
-
O6 = Basic stability: Material (Non conform management - Traceability)
-
O7 = Pull flow (kanban system)
-
O8 = Continuous flow (takt time calculation)
2. COPY & IMPROVE ASSOCIATED BEST PRACTICES
Practice from: Nanjing factory
Contact: Tony PAN
What: How OPEX inspired us to take action?
Gains: many performances improvements within one year (reduction of human to, improvement of lines efficiency...)
Assessment level: C

Practice from: Xavier Bataille
Contact: Xavier Bataille
What: To highlight sentence by sentence on the grid what the organization has reached (in green), and has not reached (in red)
Gains: Ease the information collection. Improve assessment report
Assessment level: /

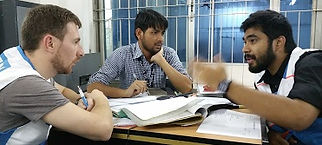
Practice from: CI team
Contact: Xavier Bataille
What: For a good assessment you have to mix between on the field gembawalks and into office questioning to collect evidences and speak with datas for the report
Gains: Improve quality of the report and facilitate the action plan
Assessment level: /
3. GO FURTHER WITH OUR COACHING OFFER
Please contact: TEC / CMW factories
4. VALIDATE YOUR SKILLS
Competency = To assess any organization [CICA]