PRODUCTION LINE OPTIMIZATION
1. LEARN BY YOURSELF & CHALLENGE YOUR WAY OF DOING
WHY
To increase Operators, Customers and Shareholders satisfaction
WHAT
Use the methodical process to optimize a production line.
HOW
1. Go on the field, be at the service , listen & work together with operators on the field. Make their job easier. They are the one to make the added value.
2. Create the dreamed workstation: optimize safety, gesture, position... Each workstation reach the ergonomics rules, comfortable, no interference + Eliminate Wastes reducing the variability on the production line. Component have to be supplied near the mounting point & the hand of the operator, In frontal dynamic supply, ready to be mounted (no polybag...), In small boxes. If variabilities can’t be totally eliminated, they are concentrated in the logistics + Implement standardized work. + implement visual management to clarify standards, responsibilities and piece flow (every cm² too big is wastage).
3. Create the dreamed line: Implement continuous flow or 'one piece flow' and define 'I' shape or 'U' shape. The distance between 2 pieces is standardized + Start auto-control (only good pieces go to the next workstation). It permits to detect 100% defect, as soon as it is produced. Analyse & solve it quickly. Allow to isolate non conform piece before next step. Connect it to Quality internal management (trained operator, standard with autocontrol, OK start, Rework station, Red box, Andon system).
4. Calculate the Takt Time: Satisfy the customer demand through flexibility & agility. Every gap to the customer demand will lead to: either a customer shortage, either a stock of finish product therefore non added value.
TT = Production time (opening - planned stop) / Qty of pc requested
Weekly demand: 5400 pces, Opening time: 5 days, 2 shifts of 8 hours Planned stop: 20 mn of change over / team, 10 mn of meeting (top 5 + 5s) / team. TAKT TIME = 50 seconds
5. Produce the customer demand with the necessary operators.
Nb of operators = Work Content / Takt time
Work content is the sum of all operating time for a product.
6. Manage the skills of your team actively
7. Monitor the performance. Implement performance boards & problem solving routines.
8. Practice line balancing per product to respect the takt time.




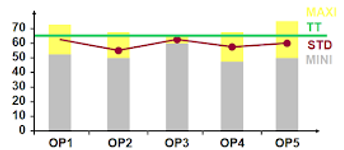
BENEFITS
-
Increase the operator satisfaction (better security, better ergonomy, kill all the non added value, increase their bonus...)
-
Increase the customer satisfaction (increase the quality, lower prices, less shortage, better flexibility, higher volumes...)
-
Increase the shareholder satisfaction (increase the profitability, decrease the investments, increase the turn over...)
2. COPY & IMPROVE ASSOCIATED BEST PRACTICES
4. VALIDATE YOUR SKILLS
Competency = to...
5. EVALUATE YOUR ORGANIZATION
Assessment =
Chapter =